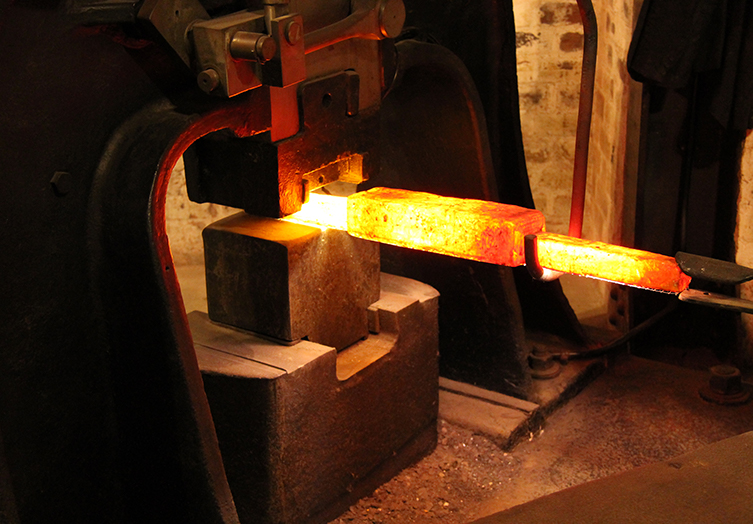
Forging
EURO METRICS forging- High-quality and cost-effective forged parts start here.
- Not all forged parts are created equally. You shouldn’t have to sacrifice quality to save money. Nor should you have to spend extra to get precision crafted metal forgings. At Euro Metrics, you can have both quality and competitive pricing for your next forged metal project.
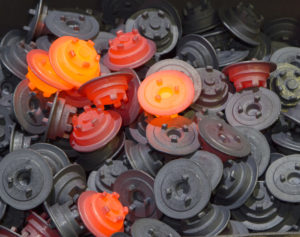
Hot forging part of automotive industry
BEST-IN-CLASS FORGED COMPONENTS
- ISO Certified Metal Forging
- We don’t just promise high-quality forged parts – we deliver them, thanks to our global network of ISO certified suppliers and the on-site support of our in-house project engineers. Lighting, automotive, transportation, electrical and power, construction and agriculture, and e-mobility OEMs rely on Euro Metrics for exacting steel forged components, products, and parts.
HOT, WARM AND COLD FORGING
- Forged Metal Solutions from Prototype to Production
- Metal forming and shaping is an exacting process, requiring calculated engineering and precision manufacturing to ensure that it’s done right. Euro Metrics supports a wide range of forged manufacturing technologies and metals, including stainless steel, carbon steel, and titanium. In addition, we design, develop, prototype, and forge all shapes, sizes, and quantities of metal and alloy parts.
REDUCED LEAD
- Metal forged parts delivered on time, every time
- We do more than metal forging. We’re supply chain experts who are committed to continuous, no-interruption production. That means we have a ready inventory of metals and alloys for no-hassle forged metal parts that are made – and delivered – to your specifications.
Get Started
- Need precision forged parts in a ferrous or non-ferrous alloy? Let Our Sales Team Help
- Forging is a manufacturing process that involves the shaping of metal by using localized compressive forces – traditionally, from a hammer against an anvil, and more often today utilizing a die. Euro Metrics provides three types of forging processes: hot forging, warm forging and cold forging.
- Widely used in mechanisms and machines wherever a component requires high strength, forging can produce a component that is stronger than an equivalent cast or machined part.
- The Benefits of Forging
- Forging offers uniformity of composition and structure
- As the metal is shaped during the forging process, its internal grain deforms to follow the general shape of the part. As a result, the grain is continuous throughout the part, giving rise to a piece with improved strength characteristics. This strengthens the resulting steel product, particularly in terms of impact and shear strength.
- Strong and Reliable
Forged metal parts offers superior strength compared to other metal working processes. The high strength is a result of the tight grain structure of the forged metal. The strength and reliability of forged products go beyond the casted, fabricated and welded products. Forged products can maintain its performance on a wider temperature range due to the grain structure.
- Highly Cost-Effective
- The forging process offers a significant cost advantage, particularly in precision metal manufacturing in high volume production runs. The materials used in forging are less expensive compared to other materials used in metalworking processes. In addition, it requires fewer secondary operations in most cases. With its high precision ability, the finish material can be obtained with exact dimension and good surface finish. Which is why it requires a low machining giving a way to cost-effectiveness.
- Difference Between Hot Forging and Cold Forging
- Hot Forging process involves extreme heat, with the desired temperature depending on the type of metal. The average temperature required for deforming steel is approximately 1150 degrees Celsius; for aluminum alloys, the temperature range is 360 to 520 °C; for copper alloys, the range is 700 to 800 °C. The high temperature is necessary to prevent strain hardening during deformation. Hot forging is typically a better choice for steel forgings used in technical applications and for deforming metal that has a high formability ratio. One the downsides of hot forging is that it offers less precise tolerances, the potential for warping during cooling and the possibility of an adverse reaction between the metal and the surrounding environment.
- Cold Forging deforms metal while it is below its recrystallization point. Cold forging is preferred when the metal is softer like aluminum. This process typically is less expensive than hot forging and the end product requires little, if any, finishing work. In some case when aluminum is cold forged into a desired shape, it is heat treated to strengthen the piece. This is called “tempering.”
- Despite the word “cold,” cold forging occurs near room temperature. The most common metals in cold forging applications are usually standard or carbon alloy steels. One of the most common types of cold forging is a process called impression-die forging, where the metal is placed into a die that is attached to an anvil. The metal is then hit by a descending hammer and forced into the die. Depending on the product, the hammer may be dropped on the metal numerous times in a very rapid sequence.
- The Advantages of Hot Forging Include
- Main advantage: As the metal is deformed the strain-hardening effects are negated by the recrystallization process
- Parts possess increased ductility which makes them desirable for many configurations
- Porosity-free surface quality enables a wide range of completion operations such as polishing or surface treatment
- Efficient process when working with harder metals such as steel
- The Advantages of Cold Forging Include
- Considered eco-friendly compared to other manufacturing processes
- High quality of the surface material
- Consistency of each part manufactured
- Efficient usage of material
- Materials used for Forgings
- Aluminum
- Brass
- Copper
- Titanium
- Zinc
- Carbon Steel
- Stainless Steel