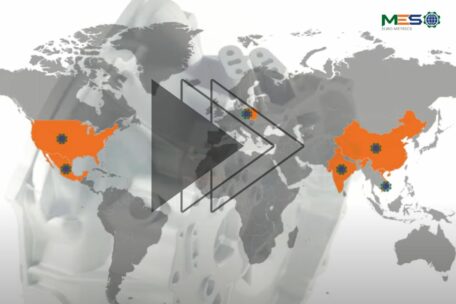
Our new movie
See what our work looks like! How are we doing? How do we source suppliers and who do we provide our services to? Today we talk about our activities - watch the video, meet
Read MoreAluminium castings have been used in industry for almost two centuries. Aluminium has features that make it a highly desirable material for use in mechanical parts. Aluminium is a lightweight, easy to process metal with good thermal and electrical conductivity. But it also has a few disadvantages. It oxidizes quickly and wears quickly. Because it is relatively soft, it is prone to dents, scratches and abrasions. Adding a protective coating is one way of protecting aluminium.
Anodizing is a process in which the aluminium surface is artificially oxidized to form a protective coating. Oxidized aluminum is extremely durable. It is chemically inert, as evidenced by its relationship to alternative forms with the same chemical structure (Al2O3), such as sapphire ceramics or aluminium oxide. Dimensionally, anodizing can effectively increase the surface thickness of parts to almost 0. 13 mm. Anodizing is usually the most suitable protective coating for aluminium parts in opto-mechanical applications. Aluminium anodisation is defined in accordance with MIL-STD-8625, which defines three basic types:
– Chromium (type I),
– Sulphur (type II)
– Hard (type III).
Anodizing is one of several possible ways of protecting aluminium components against rapid wear. Other methods are: nickel, gold and chrome plating, chemical foil coating, powder coating. Thanks to anodizing, our suppliers secure finished products and prepare them for subsequent processes, including painting or assembly. It is therefore worthwhile to cooperate in this area with professionals whose deliveries are provided by EURO METRICS.
If you are looking for an aluminium parts supplier, please contact us. We provide full support at every stage: from design through production and coordination of the entire supply chain directly to your production line.
See what our work looks like! How are we doing? How do we source suppliers and who do we provide our services to? Today we talk about our activities - watch the video, meet
Read MoreEV – a developing technology that changes the automotive market There are more and more electric vehicles, which are constantly gaining supporters. We can see many factors that are responsible for this state of
Read MoreLight Fairs 2023 - let's meet! Increasing luminous efficiency, smart cities, IoT - lighting fixtures have long ceased to be assessed in terms of their basic function. Today, apart from design and efficiency, comercial
Read More